ATEX CERTIFICATED NON-SPARKING ALLOY AND DIFFERENCE FROM OTHER TYPES OF ALLOYS
ALLOYS | ZONE 0/20 | ZONE 1/21 | ZONE 2/22 | SPECIFICATION |
---|---|---|---|---|
BERYLLIUM COPPER | + | + | + | Carcinogenic Contrast Ratio High Fragile Contains Iron (Fe) |
ALUMINUM COPPER | - | + | + | Contrast Ratio High Fragile Contains Iron (Fe) |
TEKTAS | + | + | + | %100 Resistance No Beryllium No Iron |
Non-sparking hand tools are manufactured with different types of alloys all over the world. The most common ones are beryllium copper and aluminium copper.
What is important is to be able to maintain non-sparking feature whilst attaining desired hardness and preventing fragility. As exproof products are generally costly and breakages are not covered under warranty, the buyers face hard time when such incidents occur.
Usually, the hardness and resistance in alloys is attained through the use of beryllium. However, when the manufacturers have increased the ratio of beryllium for more resistance, the ratio of fragility has also gone up.
As beryllium is considered a hazardous material by the World Health Organisation (WHO), it has not been possible to manufacture alloy with technically correct ratio of hardness.
Due to the problems with the use of beryllium, small number of manufacturers have attempted to come up with a different type of alloy. This is how aluminium alloy was made but desired level of hardness has not been achieved yet. That is why, this type of alloy is still in Zone II.
As a result, despite all efforts no manufacturer in the world has been able to come up with the type of fully resistant alloy that contains no beryllium but at the same time is usable in all Zones.
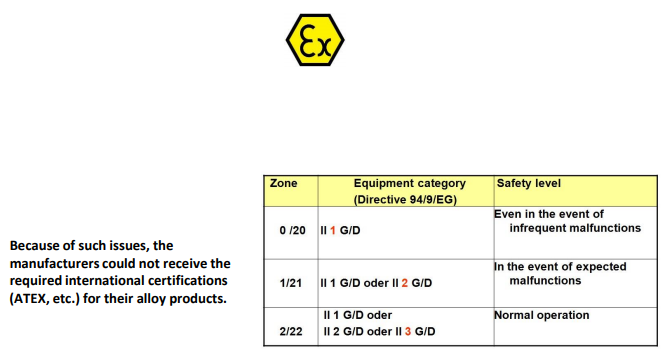
Although some of the manufacturers do not have the ATEX certification, they still use atex (ex) logo on their websites, which seriously misleads the exproof market. Once questioned, these manufacturers claim ‘their products are compatible with ATEX’ and can never present any document or certification on ATEX. Manufacturing products compatible with ATEX requirements is totally different from getting the actual certification.
The ATEX Certification is an international document that is granted after the product is subjected to numeroustests and experiments.
The ATEX Requirements also bring along serious liabilities to the manufacturers. In addition to several tests and personnel training, all products that are manufactured under the directives of the certification must include ATEX marking. These markings should include several data such as certificate number, group code, equipment code, zones, year of manufacture and code of the manufacturer. These codings differ from one product to another.
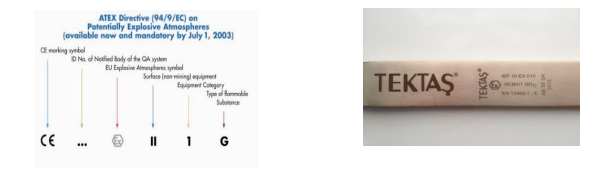
TEKTAS Safety Tools alloy is the only non-sparking alloy in the world that can be used in all Zones. This patented product contains no beryllium, carries ATEX certification with 100 percent resistance achievement. Our products are special as they fully comply with ATEX Requirements and are awarded with ATEX Certification.
The alloys of our products never contain Beryllium (Be), which is classified as hazardous and carcinogenic by the WHO.
Another special feature of our products is that they come with a 7-year warranty and as a first in the world, any breakage due to misuse is covered by this warranty. This type of coverage brings additional value to our clients as they invest in such costly equipment.
Furthermore, as required by law, your employees who work in a flammable work environment shall be trained in using ATEX certified Exproof products and Zones. Thus, each employee should be able to analyze the risk by himself.
As Tektas Safety Tools, we are happy to offer you this applied training on flammable environments and use of equipment at no cost.
Tektas Family is looking forward to working with you and wishes a safe day.
EXPLOSION PROTECTION...
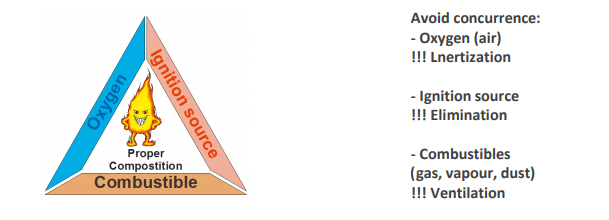
IGNITION SOURCES - EN 1127-1...
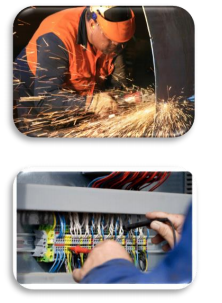
Ignition of an explosive atmosphere can be caused by various sources:
- hot surfaces
- flames and hot gases
- mechanically generated sparks
- electrical installations
- equalizing currents, cathodic corrosion protection
- static electricity
- lightning
- electromagnetic waves (high-frequency)
- optical radiation
- ionising radiation
- ultrasonics
- adiabatic compression and shock waves
- exothermal reactions
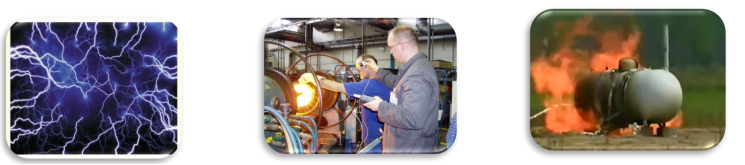
ZONES...
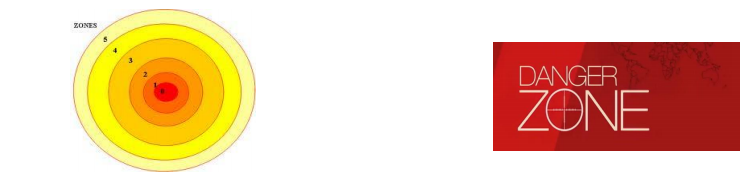
Zone 0
A place in which an explosive atmosphere consisting of a mixture with air of flammable substances in the form of gas, vapour or mist is present continuously or for long periods or frequently. |
Zone 20
A place in which an explosive atmosphere in the form of a cloud of combustable dust in air is present continously, or for long periods or frequently. |
Zone 1
A place in which an explosive atmosphere consisting of a mixture with air or flammable substances in the form of gas, vapour or mist is likely to occur in normal operation occasionally. |
Zone 21
A place in which an explosive atmosphere in the form of a cloud of combustible dust in air is likely to occur in normal operation occasionally. |
Zone 2
A place in which an explosive atmosphere consisting of a mixture with air of flammable substances in the form of gas, vapour or mist is not likely to occur in normal operation but, if it does occur, will persist for a short period only. |
Zone 22
A place in which an explosive atmosphere in the form of a cloud of combustible dust in air is not likely to occur in normal operation but, if it does occur, will persist for a short period only. |
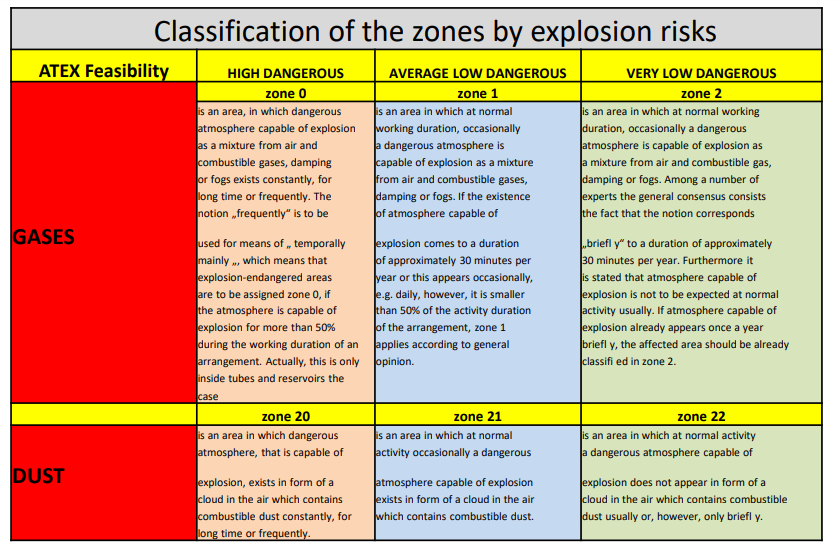
PRODUCT APPLICATION AREAS...
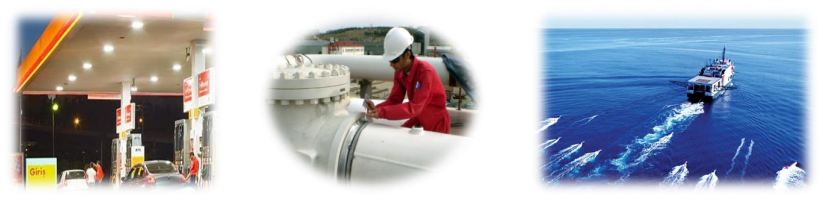
Non Sparking safety tools prevent property, life and job losses against explosions and fires during the sudden mechanical operations and interventions when they are used in processing storing, and transporting of the explosive, flammable and easily combustible materials.
Non Sparking safety tools are used for uninstallation, installation, fastening, punching, squeezing, pulling, scraping and drilling purposes.
General uses are all places with a risk of explosion, flare and combustion.
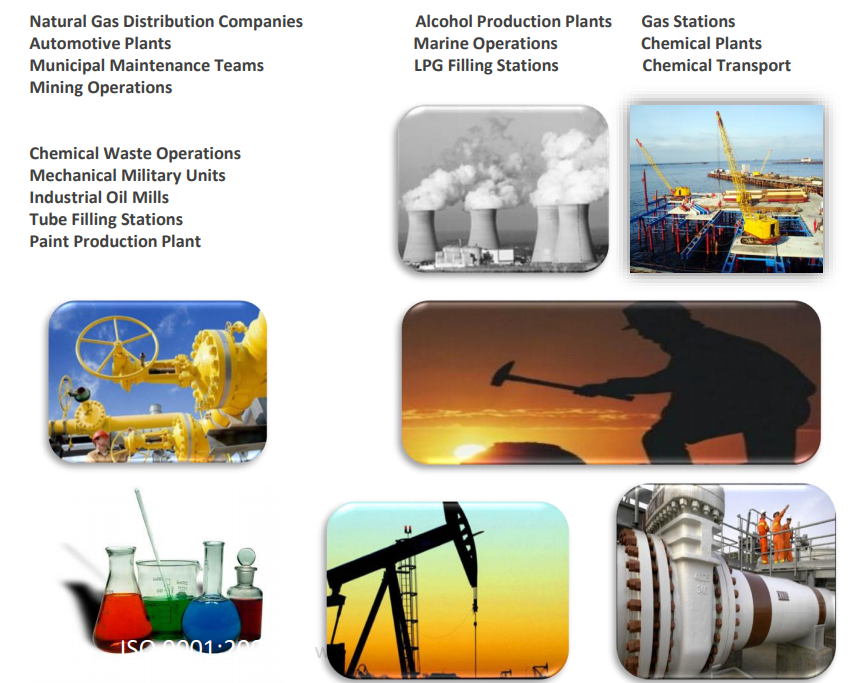